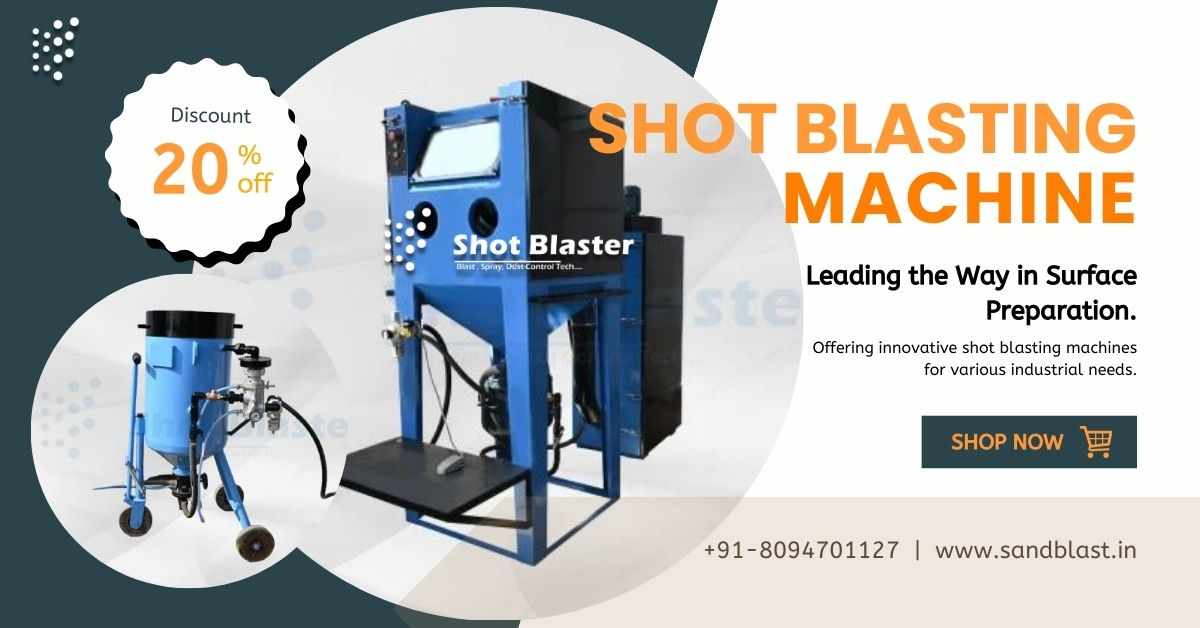
Selecting the appropriate shot blasting machine for your industry can significantly impact your operations. These machines effectively clean and prepare surfaces with the aid of small particles. Various types are optimized for specific materials and tasks. This article will outline important factors to consider when choosing a shot blasting machine, enabling you to make a well-informed decision for your business requirements.
Understanding Shot Blasting Machines
A shot blasting machine comprises several components including blast wheels, a screw conveyor, a bucket elevator, a steel shot abrasive container, and a dust collector. These elements work together in the blasting process to achieve effective surface preparation. For instance, steel shot is used for its wear resistance and cleaning efficiency. The choice of media influences the surface roughness and overall blasting results, as different shots can create varying textures.
Understanding the automatic infeed and control software within shot blasting equipment can enhance safety by minimizing manual intervention. Such systems help maintain consistent performance while reducing labor costs. High-pressure blowers and air wash cleaners contribute to the efficiency of the cleaning process by ensuring unwanted dust and debris are effectively removed. Furthermore, having a drying tunnel in the surface treatment line improves results by preparing surfaces for subsequent processes.
Replacement parts should be easily accessible to ensure the equipment's longevity and performance, leading to improved operational efficiency.
Also Check – Shot Blasting Machine | Shot Blasting Machine Manufacturer | Buy Shot Blasting Machine
Key Industries Utilizing Shot Blasting
Aerospace
In the aerospace industry, shot blasting machines are widely used for surface treatment tasks, especially for preparing steel surfaces and castings. The performance of shot blasters directly influences the quality of parts by ensuring proper surface roughness, which is necessary for paint adhesion and improved durability.
When choosing shot blasting equipment, aerospace materials often require high wear resistance and elasticity; thus, steel shot and specific abrasive containers are selected based on these criteria. The automatic shot blasting system, along with control software, boosts cleaning efficiency and lowers labor costs by reducing manual intervention. Features such as blast wheels and high-pressure blowers enhance abrasive cleaning, while dust collectors maintain a clean environment. Moreover, a surface treatment line may incorporate drying tunnels and automatic infeed systems to optimize the blasting process, yielding high-quality results.
The replacement parts for shot blast equipment are designed to meet the demanding specifications of aerospace applications, ensuring consistent performance and longevity.
Automotive
Shot blasting machines enhance the efficiency of automotive manufacturing by providing effective surface preparation, which supports paint adhesion and rust prevention. These machines use steel shot to clean and prepare automotive parts such as castings and steel surfaces. When selecting a shot blasting machine, automotive companies should consider factors like cleaning efficiency, the capability of automatic infeed systems, and the size of equipment suited for their production line.
Features like high-pressure blowers, dust collectors, and control software are important for optimizing the blasting process. Effective shot blast equipment leads to better surface roughness and wear resistance, which benefit the longevity of automotive components.
Additionally, automatic shot blasting reduces manual intervention and lowers labor costs, making production smoother. With the correct setup of blast wheels and abrasive containers, companies can expect consistent blasting results. Including a drying tunnel in the surface treatment line further ensures that parts are ready for the next steps without excess moisture affecting quality.
Also Check – https://cutt.ly/Re9OXAD3 | | https://shorturl.at/zeKzq | https://shorturl.at/oPRgI | https://rb.gy/sljqqa
Construction
The construction industry often faces challenges like surface preparation and cleaning of steel surfaces and castings. Shot blasting machines can help address these difficulties by providing effective abrasive cleaning options. Automatic shot blasting equipment, which includes blast wheels and a high-pressure blower, enhances cleaning efficiency and reduces labor costs.
The choice of a shot blasting machine directly influences the quality of surface treatment; for example, shot blasters equipped with control software can adjust the blasting process for optimal surface roughness. This focus on detail leads to better bonding of coatings or finishes. Safety considerations are important too, as proper use of a dust collector is necessary to manage airborne particles. Equipment, including bucket elevators and screw conveyors, must be checked regularly for wear resistance and efficient operation.
Additionally, it's important to minimize manual intervention to avoid accidents during the blasting process and ensure that all replacement parts are readily available. Implementing these measures fosters a safer work environment while achieving excellent blasting results.
Learn about - https://riyasingh258.stck.me/post/699684/The-Complete-Guide-to-Shot-Blasting-Machines-Principles-Types-and-Applications
Metal Fabrication
Shot blasting machines are commonly used in metal fabrication for surface preparation of steel, castings, and other metal components. These machines feature blast wheels that propel steel shot or other abrasives for cleaning and finishing, which improves the quality and durability of metal products by enhancing surface roughness. This improvement aids in better coating adhesion and increases wear resistance.
When selecting a shot blasting machine, companies should take into account cleaning efficiency, the need for automatic infeed systems, and equipment capacity such as screw conveyors, bucket elevators, and dust collectors.
Additionally, it is important to consider control software for monitoring operations and reducing manual intervention to optimize the blasting process. Labor costs and the availability of replacement parts are also significant for ensuring equipment longevity and performance. Furthermore, including components like high-pressure blowers and air wash cleaners can boost blasting effectiveness and facilitate thorough surface treatment operations.
Also Check – Shot Blasting Machine Price | Best Shot Blasting Machine
Factors for Choosing the Right Shot Blasting Machine
Material Type
Commonly processed materials in shot blasting include steel, castings, and various metals. The type of material influences the choice of shot blasting machine, as different materials require different forms of shot blast equipment to achieve desirable results.
For example, steel shot is often used for steel surfaces to ensure effective abrasive cleaning and proper surface roughness. Factors like wear resistance and the need for replacement parts should be considered when selecting equipment for specific materials. The blasting process may also involve different shot blasters or blast wheels tailored for the material being processed. Space considerations such as a drying tunnel, automatic infeed systems, and a dust collector can impact automatic shot blasting efficiency as well.
Control software is necessary for managing operations and minimizing manual intervention, while components like the high-pressure blower and screw conveyor help improve the cleaning efficiency of the surface treatment line. Proper selection based on material type helps achieve the best blasting results and maintains a cost-effective production process by reducing labor costs.
Production Volume
The current production volume for specific applications influences how shot blasters operate during the blasting process. Higher production volumes often necessitate larger shot blasting equipment, such as those with multiple blast wheels or a wide table blast. Selecting the appropriate size and type of shot blasting machine, which may include features like an automatic infeed, is based on the volume of castings or steel surfaces needing treatment.
Strategies to boost production volume include advanced control software that minimizes manual intervention and high-pressure blowers for efficient dust collection. Implementing a surface treatment line with robust cleaning efficiency can improve blasting results while using steel shot in an abrasive container.
Additionally, integrating components like bucket elevators and drying tunnels ensures a steady workflow and manages labor costs. These enhancements support consistent surface roughness and wear resistance, leading to better performance of shot blast equipment. Regular maintenance and timely replacement parts are also important for maintaining production volume and quality in shot blasting operations.
Also Check – Shot Blasting Machine Manufacturers in India | Shot Blasting Machine for Sale
Workspace Size
The dimensions of the workspace influence the selection of a shot blasting machine significantly. A smaller area may necessitate a more compact machine, while larger spaces can accommodate bigger equipment capable of processing higher volumes of castings without manual handling, thus enhancing cleaning efficiency. It's important that the size of components like bucket elevators and dust collectors aligns with the available room for optimal operation.
Additionally, safety clearances are necessary to ensure safe functioning and easy access to replaceable parts. The blasting process involves multiple components, such as high-pressure blowers and blast wheels, that require adequate spacing for effective surface treatment. With enough space, automatic infeed systems and control software can operate smoothly, whereas tight areas can limit airflow and increase wear on the machinery, potentially impacting the quality of treated materials.
By ensuring a suitable workspace, production elasticity can improve, leading to reduced labor expenses.
Upgrade your knowledge - https://riyasingh258.stck.me/post/699741/Understanding-Shot-Blasting-Processes-From-Surface-Preparation-to-Finishing
Types of Shot Blasting Machines
8-inch Shot Blaster
An 8-inch shot blaster is commonly used for surface preparation tasks in various industries such as manufacturing and construction, helping to clean steel surfaces and castings. This equipment employs high-quality steel shot for abrasive cleaning, improving surface roughness for painting or coating. Compared to larger models, the 8-inch shot blaster offers good cleaning efficiency while accommodating facilities with limited space, making it suitable for smaller production volumes.
Maintenance practices for this machine include regularly checking the blast wheels and ensuring the abrasive container is filled with steel shot. Operators should also inspect the dust collector to prevent blockages and maintain airflow, which is important for effective operations.
Automatic shot blasting systems often incorporate control software that reduces manual intervention, but performing regular checks on parts such as the screw conveyor, bucket elevator, and high-pressure blower enhances durability and reduces labor costs over time.
Finally, integrating a drying tunnel and air wash cleaner into the surface treatment line can optimize blasting results and extend the wear resistance of the equipment.
16-inch Shot Blaster
A 16-inch shot blaster offers numerous benefits over smaller models by enhancing cleaning efficiency and production capabilities. It is suitable for larger surface preparation tasks, making it perfect for industries such as automotive and aerospace, where quality surface treatment is a priority. The automatic shot blasting feature ensures consistent results, providing thorough abrasive cleaning of steel surfaces with steel shot.
Additionally, the inclusion of a screw conveyor and bucket elevator streamlines material movement, decreasing the need for manual labor. This equipment often features advanced control software for accurate operation, along with blast wheels that improve wear resistance and surface roughness. When choosing a 16-inch shot blaster, it's important to consider workspace size and production volume, as larger units may be more appropriate for spacious facilities. Compatibility with dust collectors and high-pressure blowers is also significant for performance.
Investing in a shot blast machine equipped with an efficient air wash cleaner can enhance blasting outcomes, while being aware of labor costs and replacement parts supports ongoing operations.
Benefits of Different Shot Blasters
Efficiency
The efficiency of shot blasting machines can differ based on their size and design, like the 8-inch versus the 16-inch shot blasters. Larger machines may handle bigger loads and improve cleaning efficiency, especially for surface preparation tasks on large steel surfaces or castings. Regular maintenance, including inspecting components like the bucket elevator, blast wheels, and screw conveyor, can enhance the performance of shot blast equipment.
Proper upkeep ensures the equipment, such as dust collectors and high-pressure blowers, works effectively to remove debris, contributing to better blasting results and minimizing wear issues. Operator training is important too; knowledgeable workers can adjust control software and manage the blasting process with minimal manual intervention. They are more likely to follow best practices, thereby optimizing the automatic infeed and ensuring the right amount of steel shot is used.
When everything runs smoothly, the surface roughness achieved during surface treatment lines meets the required standards, leading to less wasted material and lower labor costs.
Cost-effectiveness
When assessing the cost-effectiveness of various shot blasting machines, factors such as initial investment, long-term operational costs, and maintenance are important. Purchasing a shot blast machine, especially those with automatic infeed and blast wheels, may involve higher upfront expenses. However, these machines often enhance cleaning efficiency through improved surface preparation, leading to significant time savings.
For example, a high-pressure blower paired with an effective dust collector can minimize manual intervention, reducing labor costs. Over time, the efficiency gained from such shot blasting equipment may justify initial expenses; for instance, using steel shot and a well-designed abrasive container can lower the frequency of replacement parts needed.
Additionally, the equipment's durability, including the wear resistance of components, contributes to overall savings. An automatic surface treatment line, which offers consistent results and reduced surface roughness, can streamline operations, making it a more economical choice over time compared to basic models.
Versatility
The adaptability of shot blasting machines allows them to serve multiple industries, working with various materials such as steel castings. These machines are capable of performing various surface treatment tasks, including abrasive cleaning and surface preparation, which is important for maintaining steel surfaces.
A shot blast machine with features like automatic infeed, a bucket elevator for transportation, and a high-pressure blower can enhance cleaning efficiency by minimizing manual tasks and reducing labor costs. Selecting equipment with adjustable blast wheels and control software facilitates precise surface roughness adjustments for different projects, resulting in improved blasting outcomes. Effective dust collectors help maintain a cleaner and healthier workspace. Equipment designed for easy replacement of parts enhances durability and resistance to wear.
Choosing the Right Shot Blasting Machine for Specific Applications
Different applications require specific material types, which influence the choice of shot blasting machine. For instance, using steel shot enhances cleaning efficiency for metal castings, while softer abrasives are better for delicate items. The production volume also affects the decision; high-demand tasks benefit from automatic shot blasting equipment with features like automatic infeed and high-capacity abrasive containers, while lower volumes may only need manual shot blasters.
The size of the workspace can limit options; a smaller area may necessitate table blast systems or compact shot blasting machines, while a larger space allows for full surface treatment lines with multiple blast wheels and dust collectors.
Blasting Head Attachments and Their Importance
Blasting head attachments improve the efficiency and effectiveness of shot blasting machines by ensuring the equipment provides the right amount of steel shot for various cleaning tasks. Different types of blasting head attachments can greatly affect performance. For instance, a blast wheel designed for high wear resistance may last longer and decrease manual intervention. This can lower labor costs and enhance cleaning efficiency.
Choosing the right blasting head attachment affects the quality and finish of steel surfaces or castings. When the appropriate attachment is used, it optimizes the blasting process, achieving the desired surface roughness with improved consistency.
Additionally, using the correct equipment along with features like control software, automatic infeed, and efficient dust collectors can further enhance blasting results. Accessories may include a screw conveyor for transporting steel shot and a bucket elevator for moving materials. Additional components, like a drying tunnel or an air wash cleaner, help maintain high cleaning standards. Properly matched attachments lead to better productivity and reduce the need for replacement parts.
Tips for Maximizing the Use of Shot Blasting Machines
1. Regular Maintenance
Regular maintenance tasks for shot blasting machines include checking the blast wheels, inspecting the dust collector, and ensuring that the steel shot and other abrasives in the container are filled properly. It's important to routinely examine components like the screw conveyor and bucket elevator for wear and to clean the high-pressure blower and air wash cleaner. These checks maintain cleaning efficiency and surface roughness achieved during the blasting process.
Planning maintenance schedules can help reduce downtime; setting reminders for manual interventions and programming automatic infeed can streamline this process. Signs that a shot blasting machine needs immediate attention include unusual noises from the blast wheels, a decline in blasting results, and increased labor costs due to frequent need for repairs or replacement parts.
Regular checks during the surface treatment line operation can catch issues early, ensuring every surface preparation task proceeds smoothly and efficiently.
2. Proper Operator Training
Training programs should incorporate hands-on experience with shot blasting machines, emphasizing the safe handling of equipment such as the screw conveyor, bucket elevator, and dust collector. Operators gain an understanding of the entire blasting process, including loading steel shot into the abrasive container and managing the high-pressure blower for enhanced cleaning efficiency.
This training helps minimize risks tied to manual intervention during surface preparation tasks and ensures operators are proficient in using control software for automatic feed systems to achieve optimal blasting outcomes.
When operators receive proper training, they operate shot blasting equipment more effectively, boosting productivity. Knowledgeable operators manage blast wheels efficiently, maintain wear resistance, and optimize surface roughness for steel surfaces and castings. Adequate training also lowers the chances of accidents and cut labor costs by reducing the need for replacement parts due to mishandling.
Certification programs should be established to evaluate and confirm operator skills in using shot blasters and automatic shot blasting systems. Certifications guarantee that operators are capable of handling various components, such as the air wash cleaner and drying tunnel, resulting in a safer and more dependable blasting operation.
3. Material Selection
When selecting materials for shot blasting applications, various factors influence the performance and efficiency of shot blasting machines. The type of shot, like steel shot or other abrasives, affects the cleaning effectiveness and surface roughness achieved during blasting. Components such as the abrasive container, blast wheel, and wear-resistant parts must be strong enough to endure the harsh conditions of blasting.
In industries like automotive or steel fabrication, the compatibility of materials such as castings with equipment affects the effectiveness of surface preparation tasks. Equipment featuring automatic infeed or high-pressure blowers may need specific materials to ensure smooth operation. The cost-effectiveness of the blasting process often relates to reduced labor expenses and the need for manual intervention when compatible materials are used.
Additionally, the inclusion of control software and dust collectors can influence cleaning efficiency and the durability of replacement parts.
Finally, materials used in the surface treatment line, including drying tunnels and air wash cleaners, help achieve optimal blasting results while minimizing maintenance.
Company Using 8-inch Shot Blaster
The company using the 8-inch shot blaster focuses on preparing surfaces for steel castings. The shot blasting machine cleans the steel surface through a combination of blast wheels and steel shot, removing contaminants and achieving a desired surface roughness. Implementing automatic shot blasting equipment reduces manual intervention, leading to improved cleaning efficiency and consistency in results.
This advanced equipment, including a screw conveyor and abrasive container, allows for seamless material handling, while a high-pressure blower and air wash cleaner enhance the abrasive cleaning process. The integration of control software ensures that operations align with industry standards. With features like a bucket elevator and drying tunnel, the machine optimizes production flow and minimizes labor costs. The use of durable replacement parts increases wear resistance, further contributing to cost-effectiveness.
Company Using 16-inch Shot Blaster
The company has identified various applications for the 16-inch shot blaster, including surface preparation tasks for steel castings. They use shot blast equipment to enhance surface roughness and improve wear resistance, making it suitable for handling different types of castings. The efficiency and performance of the 16-inch shot blaster are evaluated by comparing its cleaning efficiency and blasting results against other equipment sizes in their treatment line.
Metrics analyzed include the speed of the blasting process and the impact on labor costs due to reduced manual intervention. Since implementing the 16-inch shot blaster, the company has experienced benefits like increased productivity, thanks to automatic infeed and the integration of control software. The shot blasting machine's features, such as blast wheels and bucket elevator, help streamline operations.
They also appreciate the cost savings from fewer replacement parts and better control over their abrasive container and dust collector systems.
Additionally, the use of a high-pressure blower and air wash cleaner enhances the overall efficiency of the surface treatment process.
See it more - https://vocal.media/lifehack/top-quality-shot-blasting-solutions-for-superior-surface-finishing
Summary
Selecting the appropriate shot blasting machine is important for optimizing productivity and achieving desired surface finishes in various industries. Factors to consider include the specific application, material types, and surface requirements.
Different machines, such as air blast, wheel blast, and automated options, offer varying processes and efficiencies. Air blast machines are versatile and suitable for delicate work, while wheel blast machines are ideal for high-volume applications.
The size and design of the machine should match the production space and component dimensions. Additionally, maintenance requirements, energy consumption, and safety features are significant in the selection process.
Write a comment ...