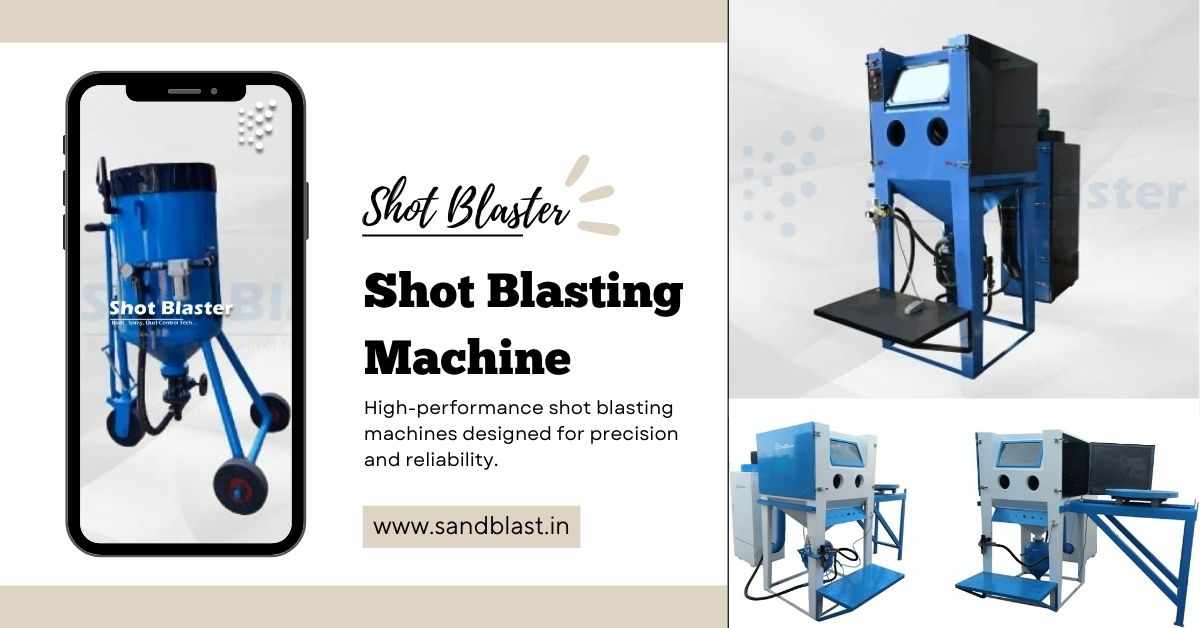
Surface preparation plays a critical role in ensuring the success of any shot blasting process. Without proper preparation, the end results may be compromised, leading to issues such as poor coating adhesion, uneven finishes, or suboptimal surface profiles. Below, we outline the most effective surface preparation techniques to guarantee optimal shot blasting results, focusing on best practices, technical insights, and essential steps.
Understanding the Importance of Surface Preparation
Before diving into specific techniques, it is important to recognize why surface preparation is crucial. Proper preparation removes contaminants such as rust, mill scale, oil, and grease, creating a surface that is clean, textured, and ready for shot blasting.
This process enhances the lifespan and quality of subsequent coatings or finishes while ensuring compliance with industry standards.
Step-by-Step Surface Preparation Process
1. Initial Surface Assessment
Before beginning the preparation process, conduct a thorough assessment of the surface condition. This step identifies:
Contaminants such as oil, grease, or corrosion.
Surface irregularities like burrs, weld spatter, or protrusions.
The desired surface profile based on project specifications or coating requirements.
By analyzing these factors, the correct preparation techniques can be selected to meet performance criteria.
Gain Insights - https://riyasingh258.stck.me/post/699684/The-Complete-Guide-to-Shot-Blasting-Machines-Principles-Types-and-Applications
2. Cleaning to Remove Contaminants
A clean surface is essential for effective shot blasting. Employ one or more of the following methods based on the type and extent of contamination:
Degreasing: Use industrial degreasers or solvents to eliminate oil, grease, and other organic residues. Alkaline cleaners are highly effective for heavy grease buildup.
Steam Cleaning: This method removes stubborn contaminants, particularly when dealing with machinery parts or heavily greased surfaces.
Solvent Wiping: For smaller areas, manual solvent wiping with lint-free cloths is an efficient solution.
3. Rust and Scale Removal
For surfaces affected by rust or mill scale, additional preparation steps are required to achieve a clean and uniform substrate. Techniques include:
Wire Brushing or Scraping: Effective for removing loose rust and dirt. While manual, this is often necessary for small or intricate areas.
Chemical Descaling: Acid-based solutions can dissolve rust and scale, but thorough neutralization is crucial to prevent post-treatment corrosion.
Mechanical Abrasion: Grinding or sanding with abrasive discs is another reliable option for smaller surfaces or localized corrosion spots.
4. Surface Profiling
The correct surface profile is essential for maximizing the bond between coatings and substrates. Profiles are typically measured using techniques such as replica tape or surface roughness gauges. The desired profile depends on factors like the coating type and application environment.
For thin coatings, a finer profile ensures smooth coverage.
For thicker or industrial coatings, a deeper, more pronounced profile may be necessary to enhance adhesion.
5. Masking and Protecting Sensitive Areas
To prevent damage to sensitive areas or components, apply masking materials such as:
Tape or Film: Ideal for small, localized areas.
Rubber Sheets or Covers: Protect larger regions or surfaces that do not require portable shot blasting machine for small workshops.
Custom Fixtures: For complex geometries, tailored protective fixtures can provide optimal coverage.
Ensure masking materials are compatible with the blasting media and do not leave adhesive residues.
6. Inspecting for Surface Readiness
Once cleaning and profiling are complete, conduct a final inspection to ensure the surface is fully prepared for shot blasting. Use the following techniques:
Visual Examination: Look for visible contaminants, uneven profiles, or uncleaned areas.
Surface Cleanliness Tests: Perform adhesion tests, dust tests, or salt contamination checks to verify readiness.
Shot Blasting Techniques for Superior Results
With the surface properly prepared, the shot blasting process can achieve superior results. Key considerations include:
1. Selecting the Appropriate Blasting Media
The choice of blasting media significantly impacts surface preparation outcomes. Common media types include:
Steel Shot: Suitable for heavy-duty applications, providing a smooth and polished finish.
Steel Grit: Ideal for aggressive cleaning, removing tough coatings, or producing angular profiles.
Glass Beads: Non-abrasive and best for achieving a satin or matte finish.
Aluminum Oxide: Effective for removing paint, rust, or scale without excessive wear on the substrate.
Match the media type and size to the project requirements to ensure consistent and effective blasting results.
Keep reading - https://riyasingh258.stck.me/post/699735/Choosing-the-Right-Shot-Blasting-Machine-for-Your-Industry
2. Optimizing Equipment Settings
Proper calibration of shot blasting equipment ensures consistent surface preparation. Focus on the following parameters:
Blasting Pressure: Adjust to suit the substrate material and desired surface profile. Excessive pressure can damage softer substrates, while insufficient pressure may result in incomplete cleaning.
Media Flow Rate: Ensure a steady flow to avoid uneven coverage.
Nozzle Angle: Maintain an angle between 45–90 degrees, depending on the surface type, to achieve uniform impact and coverage.
3. Monitoring Media Condition
Blasting media degrades over time, impacting performance. Regularly inspect and replace worn media to maintain consistent results. Recycling systems, if available, can reduce waste and lower costs without compromising quality.
Post-Blasting Surface Preparation
After shot blasting, additional steps may be necessary to ensure the surface is ready for coating or finishing:
1. Dust and Residue Removal
Residual dust or debris can hinder coating adhesion. Use the following methods to remove all traces:
Compressed Air: Quickly eliminates loose particles from the surface.
Vacuum Cleaning: Ensures thorough removal of fine dust, especially in confined spaces.
Dry Cloth Wiping: Effective for smaller areas or low-dust applications.
2. Surface Inspection
Conduct another inspection to confirm the surface profile meets project specifications. Tools like profile gauges, gloss meters, or adhesion testers can provide detailed verification.
3. Immediate Coating Application
Apply coatings or finishes as soon as possible after blasting to prevent flash rusting or contamination. Delays can compromise the effectiveness of surface preparation efforts.
Common Challenges in Surface Preparation and How to Overcome Them
While proper surface preparation ensures optimal results, challenges can arise. Here are common issues and their solutions:
Residual Contaminants: Use multiple cleaning methods or repeat steps as necessary to eliminate stubborn residues.
Inconsistent Profiles: Adjust blasting pressure or media size to achieve uniformity.
Flash Rusting: Use rust inhibitors or apply primer coatings immediately after blasting.
Conclusion
By following these detailed surface preparation techniques, shot blasting processes can achieve unparalleled precision and quality. From initial cleaning to final inspections, every step is crucial in delivering surfaces that meet industry standards and project requirements.
Proper preparation not only enhances the effectiveness of shot blasting but also ensures long-lasting, high-performance results.
For more information visit the URL - https://www.sandblast.in/product/Portable-shot-blasting-machines
Write a comment ...