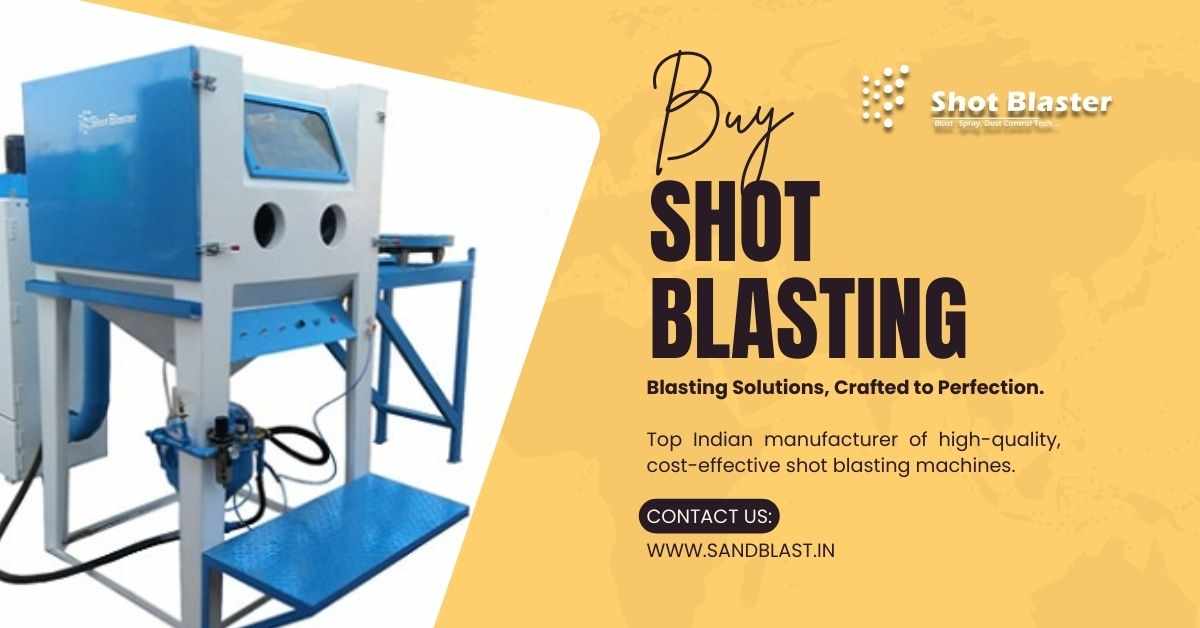
Shot blasting machines are essential tools in industries that require surface preparation, cleaning, or strengthening of metal components. These machines help remove impurities, paint, rust, or other coatings, leaving surfaces ready for further processing. However, like any other mechanical system, shot blasting machines are prone to operational issues that can disrupt productivity and result in costly downtime.
This comprehensive guide outlines common problems, troubleshooting methods, and preventive measures to help you maintain your shot blasting machine and ensure its optimal performance.
Understanding Common Issues with Shot Blasting Machines
1. Machine Won’t Start
When your hanger type shot blasting machine fails to start, it often indicates electrical or mechanical issues. Common causes include:
Power Supply Problems: Loose or damaged power cables, tripped circuit breakers, or insufficient voltage can prevent the machine from powering up.
Motor Malfunctions: Faulty motors or worn-out brushes can impede startup.
Control Panel Errors: Malfunctioning relays, sensors, or emergency stop switches may trigger a shutdown.
2. Uneven Blasting Results
Uneven or inconsistent surface blasting can significantly impact production quality. This issue is usually caused by:
Worn-Out Components: Blast wheels, blades, or control cages that are excessively worn can disrupt abrasive flow and coverage.
Improper Abrasive Distribution: Incorrect abrasive quantity or quality may lead to uneven results.
3. Reduced Efficiency
When your machine operates below optimal performance, it often results in extended cycle times and higher operational costs. Contributing factors include:
Clogging of Abrasive Pathways: Accumulated debris or improper abrasive media can block flow, reducing impact.
Dust Collector Malfunction: A poorly functioning dust collection system can reduce visibility and compromise blasting performance.
4. Overheating of Components
Shot blasting machines generate substantial heat during operation, making overheating a frequent concern. Key reasons for overheating include:
Inadequate Lubrication: Lack of lubrication in moving parts increases friction and heat.
Blocked Airflow: Dust and debris blocking ventilation can trap heat inside the machine.
5. Excessive Vibrations During Operation
Excessive vibrations can damage the machine and lead to unsafe working conditions. Common causes include:
Misaligned Components: Unbalanced blast wheels or misaligned parts can cause vibrations.
Loose Bolts or Fasteners: Regular operation may loosen components, leading to instability.
Click for more - https://riyasingh258.stck.me/post/699735/Choosing-the-Right-Shot-Blasting-Machine-for-Your-Industry
Step-by-Step Troubleshooting Guide
1. Conduct a Preliminary Inspection
Before addressing any issues, perform a thorough inspection. Follow these steps:
Disconnect Power: Ensure the machine is powered off and disconnected to avoid accidents.
Visual Check: Look for loose bolts, disconnected wires, or visible wear and tear.
Review Maintenance Logs: Check for any recurring issues documented during previous inspections.
2. Diagnose Electrical Systems
Electrical issues are among the most common reasons for machine failures. Here’s how to address them:
Check Circuit Breakers: Reset any tripped breakers and test the power supply using a multimeter.
Inspect Wiring: Look for frayed wires, loose connections, or damaged insulation. Replace any faulty wiring.
Test Motors and Sensors: Ensure that the motor is receiving adequate voltage and that all sensors are functional. Replace or recalibrate faulty components as necessary.
3. Address Mechanical Wear and Tear
Mechanical components are subject to wear over time, affecting performance. Follow these steps to troubleshoot:
Inspect Blast Wheels and Blades: Examine these parts for wear or cracks. Replace them if they show significant deterioration.
Lubricate Moving Parts: Use manufacturer-recommended lubricants to minimize friction and heat buildup.
Tighten Loose Components: Secure all bolts, fasteners, and structural parts to reduce vibrations.
4. Optimize Abrasive Flow
The quality and flow of abrasive media are critical for consistent results. Here’s how to manage abrasive issues:
Calibrate Abrasive Flow Rate: Adjust the machine settings to ensure the correct flow rate for your application.
Remove Contaminants: Inspect and clean the abrasive media, removing impurities or clumps that can disrupt flow.
Replace Worn Parts: If the abrasive control cage or distributor is damaged, replace them to restore proper flow.
5. Check Dust Collection System
A functional dust collection system is essential for maintaining efficiency and a clean working environment. Troubleshoot by:
Cleaning or Replacing Filters: Dirty filters restrict airflow and reduce suction. Clean them regularly or replace them as needed.
Inspecting Ducts and Connections: Ensure all ducts are clear of blockages and properly sealed to prevent leaks.
Preventive Maintenance Best Practices
1. Establish a Routine Maintenance Schedule
Set up regular maintenance intervals based on the machine’s operating hours and manufacturer guidelines. Include cleaning, lubrication, and inspections in your schedule.
2. Use OEM Parts for Repairs
Always opt for original equipment manufacturer (OEM) parts to maintain compatibility and ensure longevity. Non-OEM parts may compromise performance or cause damage.
3. Train Your Team
Ensure that all operators and maintenance personnel are properly trained to handle the machine. They should understand safety protocols and basic troubleshooting techniques.
4. Maintain a Maintenance Log
Document all repairs, inspections, and maintenance activities. A detailed log helps identify recurring problems and track the machine’s overall performance.
Continue reading - https://riyasingh258.stck.me/post/699684/The-Complete-Guide-to-Shot-Blasting-Machines-Principles-Types-and-Applications
Conclusion
By understanding common issues and implementing the outlined troubleshooting steps, you can ensure that your shot blasting machine operates smoothly and efficiently. Proactive maintenance and timely repairs not only reduce downtime but also extend the lifespan of your equipment.
Remember, the key to keeping your shot blasting machine in top condition lies in combining routine inspections, proper training, and the use of high-quality components. Implement these practices today and experience the benefits of consistent and reliable performance in your industrial operations.
Write a comment ...