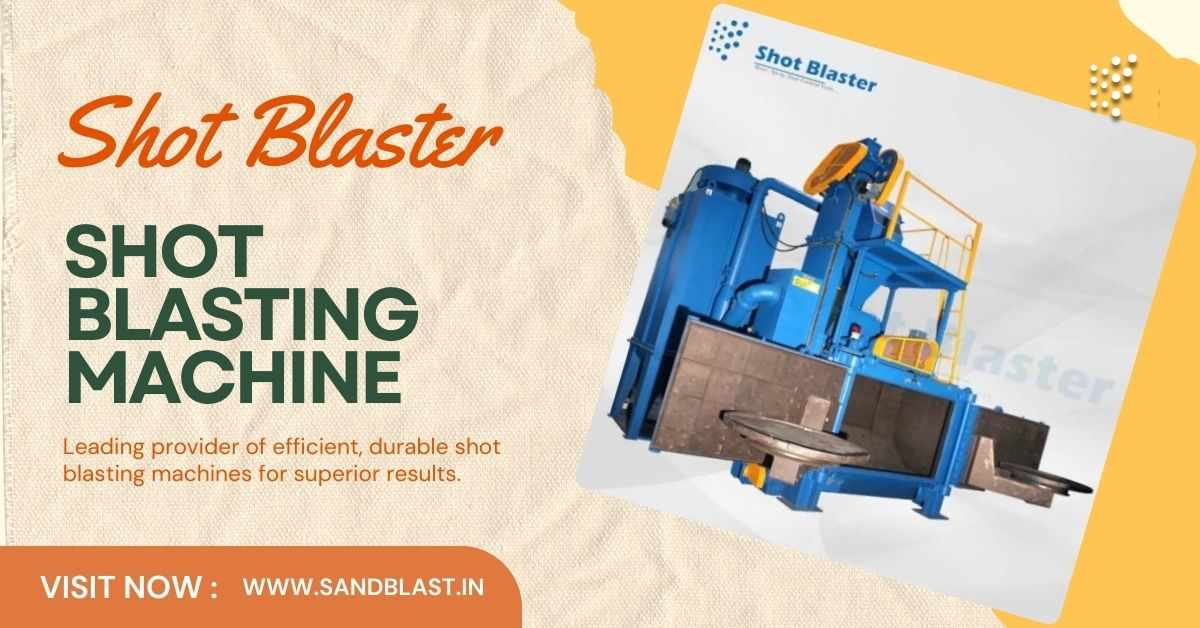
Compare shot blasting with other surface treatment methods like sandblasting and laser cleaning. Discover their processes, benefits, and industrial applications.
1. Introduction
Surface treatment plays a crucial role in industrial processes, ensuring materials are prepared for further processing or finishing. Among the many techniques available, shot blasting stands out as a popular choice. This article delves into a comparative analysis of shot blasting and alternative surface treatment methods to help industries make informed decisions.
2. Understanding Shot Blasting
Definition and Process of Shot Blasting
Shot blasting involves propelling abrasive materials, such as steel shots or grits, at high velocity against a surface to remove impurities and achieve a clean, smooth finish. This technique is widely used for Surface Preparation with Shot Blasting before coating or painting.
Types of Shot Blasting Techniques
Wheel Blasting: Utilizes a centrifugal wheel to accelerate abrasive material, ideal for large-scale operations.
Air Blasting: Uses compressed air to propel abrasives, offering precision for smaller tasks.
Benefits of Shot Blasting
Enhanced Surface Adhesion: Prepares surfaces for coatings, improving durability.
Efficiency: Quick and cost-effective for large-scale industrial applications.
Discover more - https://riyasingh258.stck.me/post/699684/The-Complete-Guide-to-Shot-Blasting-Machines-Principles-Types-and-Applications
3. Overview of Other Surface Treatment Methods
Sandblasting
This method uses sand or similar abrasive materials to clean or texture surfaces. While effective, it can generate significant dust and requires proper safety precautions.
Chemical Etching
A chemical solution removes contaminants and prepares the surface. This method is precise but less environmentally friendly.
Grinding and Polishing
Mechanical tools smooth and polish the surface, typically for aesthetic finishes or small-scale projects.
Laser Cleaning
A non-contact method that uses laser beams to remove surface contaminants. Although highly effective, it is expensive and best suited for specialized applications.
4. Shot Blasting vs. Other Methods: Key Comparisons
Efficiency and Time Requirements
Shot blasting is faster for large surfaces compared to methods like grinding or chemical etching, which require more time and labor.
Surface Quality and Consistency
Shot blasting ensures a uniform profile, making it superior for applications needing consistent surface preparation.
Suitability for Different Materials
While Industrial Shot Blasting Machine works well on metals and hard surfaces, delicate materials may require gentler methods like laser cleaning.
Environmental Impact
Shot blasting uses recyclable abrasives, making it more sustainable than chemical treatments, which involve hazardous waste.
Study more - https://riyasingh258.stck.me/post/699741/Understanding-Shot-Blasting-Processes-From-Surface-Preparation-to-Finishing
5. Applications and Industry Use Cases
Automotive and Aerospace Industries
Shot blasting is essential for cleaning and preparing components such as gears, chassis, and turbine blades.
Construction and Manufacturing Sectors
Used for surface preparation of steel structures, pipelines, and fabricated parts to enhance durability.
Heavy Equipment Maintenance
Removes rust, old paint, and debris from large equipment, prolonging their service life.
6. Choosing the Right Method for Your Needs
Factors to Consider
Material Type: Metals benefit from shot blasting, while delicate materials may need laser cleaning.
Project Scale: Larger projects often favor the efficiency of shot blasting.
Desired Finish: Precision tasks may lean toward grinding or laser methods.
Cost-Effectiveness and Environmental Considerations
Shot blasting provides a balance between affordability and sustainability, making it an attractive option for most industries.
7. Shot Blasting: Innovations and Trends
Advancements in Shot Blasting Technology
Recent innovations have enhanced the efficiency and precision of shot blasting. For instance, automated shot blasting systems now incorporate robotics and computer-controlled mechanisms to deliver consistent results with minimal manual intervention.
Sustainability Trends in Shot Blasting
With an increasing focus on environmental responsibility, manufacturers are developing abrasives that are recyclable and non-toxic. According to Shot Blaster, modern shot blasting machines are designed to reduce energy consumption and minimize waste production.
Integration with Digital Monitoring
Many contemporary shot blasting systems now include digital monitoring tools to track performance metrics, detect wear and tear, and schedule preventive maintenance, further boosting operational efficiency.
8. Safety Considerations in Shot Blasting and Alternatives
Protective Measures for Operators
Given the high-velocity abrasives used in shot blasting, operators must wear personal protective equipment (PPE), including helmets, gloves, and respiratory masks. These measures mitigate risks such as inhalation of fine dust or contact with flying particles.
Dust Control and Containment
Modern shot blasting setups often incorporate dust collectors to ensure a clean and safe working environment. These systems are particularly important when working in enclosed spaces.
Safety in Other Methods
Sandblasting: Requires robust containment systems due to the fine silica dust generated, which poses health risks.
Chemical Etching: Operators need protective gear to handle hazardous chemicals and avoid skin or respiratory exposure.
Laser Cleaning: While non-contact, operators must be cautious of laser beams and use specialized goggles for eye protection.
9. Future Prospects of Surface Treatment Methods
Hybrid Systems
Future surface treatment systems may combine shot blasting with other techniques, such as chemical etching or laser cleaning, to offer enhanced results. This hybrid approach could provide more tailored solutions for complex projects.
Increased Automation and AI Integration
Artificial intelligence is likely to play a key role in surface treatment, enabling systems to adapt dynamically to varying material properties and optimize process efficiency.
Sustainability as a Core Focus
As industries strive to meet stricter environmental standards, the development of eco-friendly abrasives and energy-efficient equipment will continue to be a priority.
FAQs About Shot Blasting and Surface Treatment
Q: What materials are best suited for shot blasting?
A: Shot blasting is ideal for metals, including steel, aluminum, and cast iron. It can also be used on concrete surfaces but is not recommended for delicate materials like glass or soft plastics.
Q: Is shot blasting environmentally friendly?
A: Compared to methods like chemical etching, shot blasting is more sustainable. Abrasives are often recyclable, and advanced machines minimize waste and energy usage.
Q: How does shot blasting compare with laser cleaning?
A: While shot blasting is cost-effective and suitable for large-scale projects, laser cleaning excels in precision tasks and environmentally sensitive applications.
Conclusion
In conclusion, shot blasting stands out as a versatile and reliable surface treatment method for numerous industrial applications. While other methods like sandblasting, laser cleaning, and chemical etching have their merits, shot blasting's balance of efficiency, cost-effectiveness, and environmental sustainability makes it an enduring choice.
By aligning surface treatment choices with project requirements, industries can achieve optimal results, ensuring durability and performance in their final products.
Write a comment ...