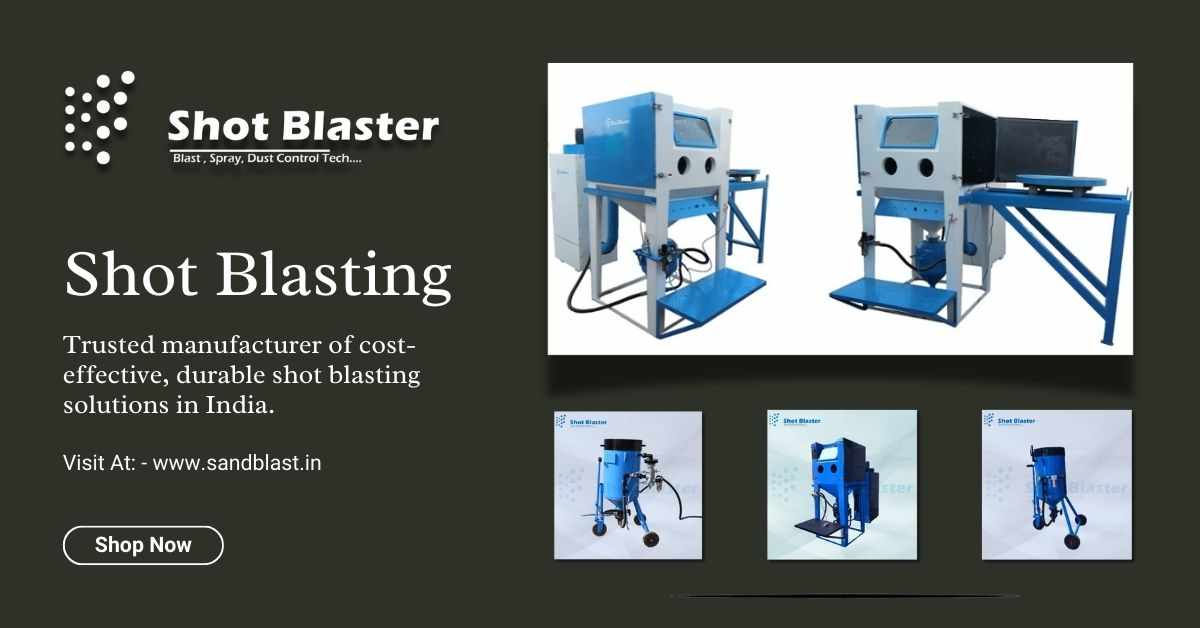
Shot blasting operates by propelling abrasive materials at high velocity to clean and prepare surfaces. Different abrasive agents, such as steel grit, aluminum oxide, or glass beads, can be used depending on the desired finish. In processes like sandblasting, both wheel blasting machines and air blasting machines effectively treat workpieces ranging from delicate materials to large metal components.
The blast wheel assembly includes a centrifugal wheel that launches the abrasive media at the workpiece, effectively addressing heavy surface contaminants or producing a smooth finish. A dust collection system is necessary to capture contaminants, ensuring a clean working environment. Various machines, including wet blasting and grit blasting systems, adapt to diverse needs, with maintenance requirements depending on the equipment type and size.
Storage hoppers organize abrasive media, while the conveyor belt moves large workpieces through the blasting process, ensuring that each item meets quality standards in industrial applications.
Also Check – Shot Blasting Machine | Shot Blasting Machine Manufacturer | Buy Shot Blasting Machine
Guide to Shot Blasting Machines: Key Components
Blast Wheel
The blast wheel significantly affects the efficiency of shot blasting machines as it propels abrasive materials, such as steel shot and aluminum oxide, at high speeds toward the workpiece. This process effectively cleans and prepares surfaces by removing heavy contaminants or creating a rough surface profile needed for preparation.
The design of the blast wheel assembly, including size and shape, affects how well the abrasive agent is delivered; an optimally designed wheel can cater to delicate work pieces and sensitive materials without causing damage. Various materials, like glass beads or plastic media, can be selected based on the desired surface finish. Regular maintenance is required to maintain optimal performance, which includes monitoring for wear, ensuring the dust collection system functions properly, and confirming that the separation system keeps the blasting media clean.
Manufacturers in India often highlight the significance of these practices to reduce operating costs and vibration levels while enhancing performance in methods like grit blasting and shot peening.
Workpiece Manipulation
Workpiece manipulation in shot blasting machines involves several techniques, including the use of conveyor belts and blast cabinets, to ensure optimal positioning and exposure. These systems facilitate efficient movement and precise placement of metal components, allowing for proper abrasive blasting for surface preparation.
Automation enhances workpiece manipulation through technologies like dynamic separation systems and automated loading mechanisms, maintaining high velocity and consistent exposure to abrasive materials like steel grit or aluminum oxide. The design significantly influences how machines accommodate large or delicate workpieces, affecting factors such as operating costs and maintenance needs. Various blasting methods, such as wheel blasting machines or wet blasting machines, are tailored to the size and shape of parts, boosting the effectiveness of blast cleaning.
An enclosed chamber with a dust collection system promotes clean operations, while specific blasting media choices, like glass beads or plastic media, achieve the desired surface finish, whether smooth or rough.
Check out details - https://riyasingh258.stck.me/post/699741/Understanding-Shot-Blasting-Processes-From-Surface-Preparation-to-Finishing
Dust Collection System
A dust collection system in shot blasting operations comprises components like filters, fans, and ducting to capture and remove contaminants generated during the blasting process. These systems manage the dust from abrasive blasting, promoting cleaner workspaces and improved air quality. For instance, when utilizing steel grit or aluminum oxide, the dust collection system effectively captures particles, preventing them from accumulating on fragile workpieces and sensitive materials.
This boosts both the efficiency and safety of shot blasting machines, lowering the risk of respiratory issues for workers and ensuring that the blast cleaning achieves the intended surface finish. When choosing a dust collection system, factors include the type of blasting method, the size and shape of the workpieces, and the maintenance needs.
Systems should accommodate both large workpieces and delicate materials, attaching securely to equipment like blast cabinets or linked to centrifugal wheel assemblies. Furthermore, operating costs, vibration levels, and the necessity for a dynamic separation system must be considered, assuring the dust collection system functions well for various materials, such as glass beads and plastic media.
Also Check – Shot Blasting Machine Price | Best Shot Blasting Machine
Types of Shot Blasting Machines
Tumble Belt Shot Blasting Machines
Tumble Belt Shot Blasting Machines are built for effective surface preparation for various workpieces. They transport metal parts on a conveyor belt through an enclosed chamber where high-velocity abrasive materials, like steel shot or aluminum oxide, are propelled by a centrifugal wheel. This process provides options for both smooth finishes and rough profiles, making it suitable for shot peening and grit blasting.
In comparison to wheel blasting and air blasting machines, Tumble Belt machines are effective for delicate and large items, offering versatility for sensitive materials. Regular inspections of the blast wheel assembly and storage hopper are necessary to avoid contaminant buildup for optimal performance. A dust collection system should be implemented to manage airborne particles and improve cleanliness. Manufacturers in India often highlight the need to monitor vibration levels and follow maintenance guidelines to extend equipment lifespan.
Blasting media, such as glass beads and plastic media, should be stored properly to maintain their size and shape.
Also Check – https://cutt.ly/Re9OXAD3 | | https://shorturl.at/zeKzq | https://shorturl.at/oPRgI | https://rb.gy/sljqqa
Hanger Type Shot Blasting Machines
Hanger Type Shot Blasting Machines feature a conveyor belt and an enclosed chamber, enabling effective handling of large workpieces and heavy surface contaminants. The workpieces are hung and manipulated, allowing the shot blasting process to cover all surfaces at high velocity. This boosts efficiency by ensuring even distribution of abrasive materials such as steel grit or aluminum oxide, achieving the desired surface finish.
They are widely used in industries needing the cleaning or preparation of metal parts, building materials, and delicate items. The option to employ various blasting media, including glass beads and plastic media, facilitates either a smooth surface finish or a rough profile, based on the application's needs. Maintenance needs are reduced due to features like a dynamic separation system and a dust collection system, which help clear contaminants while keeping operational costs reasonable.
Manufacturers in India are embracing these machines for their adaptability indifferent blasting techniques, including grit blasting and shot peening, making them suitable for a variety of material sizes and shapes.
Continuous Shot Blasting Machines
Continuous Shot Blasting Machines offer numerous benefits compared to air blasting and wet blasting machines. They are tailored for high-volume production, providing ease in processing large workpieces uniformly. With a conveyor belt system, materials move through the machine at a steady pace, ensuring consistent exposure to various abrasive materials like steel shot, aluminum oxide, and glass beads.
This results in either a smooth surface finish or a rough surface profile based on the intended result. Moreover, these machines operate with a centrifugal wheel or blast wheel assembly to propel the abrasive medium at high speeds, effectively cleaning both metal parts and delicate components. For efficient operation, manufacturers should be mindful of maintenance needs such as checking the storage hopper for abrasive material, keeping the blast cabinet clean, and monitoring vibration levels.
An effective dust collection system is necessary to remove contaminants, while the dynamic separation system works to separate used abrasive media from debris. Focusing on these aspects contributes to optimal machine performance and helps lower operating expenses.
Also Check – Shot Blasting Machine Manufacturers in India | Shot Blasting Machine for Sale
Portable Shot Blasting Machines
Portable shot blasting machines stand out because of their mobility and versatility. They can tackle a variety of projects, from cleaning large workpieces and heavy surface contaminants to treating delicate items made of sensitive materials. These machines typically use abrasive materials such as steel shot, aluminum oxide, or glass beads to achieve the desired surface finish.
This adaptability allows users to conduct abrasive blasting, sandblasting, or grit blasting in different environments, enhancing efficiency. Operating costs tend to be lower due to decreased setup time compared to stationary models. Safety is important when operating these machines. Operators should don suitable protective gear and ensure that a dust collection system is implemented to manage contaminants. Many portable machines come equipped with an enclosed chamber to reduce vibration levels and safeguard operators.
Maintenance also holds significance, including routine checks on the blast wheel assembly and making sure the storage hopper is well-sealed to prevent media loss. The centrifugal wheel design in some machines boosts performance, making them appropriate for tasks such as shot peening and blast cleaning of building materials.
Read complete guide - https://riyasingh258.stck.me/post/699735/Choosing-the-Right-Shot-Blasting-Machine-for-Your-Industry
Applications of Shot Blasting Machines
Metal Surface Preparation
When considering shot blasting techniques for metal surface preparation, factors like the type and size of the workpiece, the level of contamination, and the desired surface finish are significant. Different abrasive materials, such as steel grit, aluminum oxide, and glass beads, influence how effectively contaminants are removed.
For example, steel shot works well on heavy surface contaminants, while plastic media may be better for delicate workpieces. The effectiveness of the blasting method also depends on the equipment used, such as wheel blasting machines or air blasting machines, along with maintenance requirements to ensure high performance. Successful metal surface preparation is indicated by a smooth surface finish, the absence of contaminants, and a rough surface profile that promotes better adhesion for coatings. Techniques like shot peening can enhance the durability of metal parts, while a dust collection system helps maintain a clean work environment.
A dynamic separation system may also improve the efficiency of abrasive materials stored in a storage hopper, optimizing operating costs in the long run.
Concrete Surface Treatment
Concrete surface treatment using shot blasting offers numerous advantages. This method prepares surfaces by employing shot blasting machines that project abrasive materials like steel shot or aluminum oxide at high velocity. This creates a rough surface profile, aiding in the bonding of coatings and adhesives. Unlike sandblasting or other techniques, shot blasting effectively removes heavy surface contaminants, promoting a smooth surface finish and enhancing durability.
It is important to consider the size and shape of the workpiece. Manufacturers provide various types, such as air blasting machines and wheel blasting machines, suited for large or delicate workpieces. Maintenance requirements should also be considered, as machines like blast cabinets and wet blasting machines have unique upkeep needs. An efficient dust collection system can control vibration levels and contaminants, contributing to improved performance.
The choice of blasting media, whether plastic media or glass beads, can influence finish quality and operating costs. Selecting the appropriate blasting method ensures the desired surface finish and extends the lifespan of building materials.
Aerospace and Automotive Industries
Shot blasting machines are commonly found in aerospace and automotive sectors for preparing metal surfaces. These machines use methods such as sandblasting and abrasive blasting to obtain a specific surface finish. When selecting equipment, manufacturers consider factors like the size and shape of the workpiece, opting for either wheel blasting machines or air blasting machines.
Centrifugal wheels are advantageous for large parts due to their high velocity, whereas smaller or more delicate items may benefit from wet blasting machines that use materials like aluminum oxide or glass beads.
One challenge is managing heavy surface contaminants and achieving a consistent surface profile without harming sensitive materials. To address these concerns, innovations such as dynamic separation systems and dust collection systems are being created, helping control vibration levels and cut down on maintenance. Moreover, incorporating a blast cabinet with a storage hopper can streamline operations and reduce costs. As manufacturers in India and beyond continue to push boundaries, processes like shot peening and grit blasting are becoming more effective, ensuring superior finishes for both heavy-duty and delicate tasks.
Also Check – https://rb.gy/ii4tpg | https://rebrand.ly/SB5asln | https://rebrand.ly/SB49Ind | https://cutt.ly/Ge9OZ25U
Factors Influencing Shot Blasting Machine Selection
When selecting a shot blasting machine, specifications such as operating cost, maintenance requirements, and the type of abrasive materials, like steel grit or aluminum oxide, are important. Different blasting methods include air blasting machines, wheel blasting machines, and wet blasting machines, each suited for various applications.
The size and shape of the workpieces also dictate the choice; large workpieces might require a conveyor belt system, while delicate workpieces benefit from enclosed chambers to prevent damage. Environmental regulations, such as dust control and vibration levels, impact the decision too, guiding users toward machines with effective dust collection systems or dynamic separation systems.
For example, the use of glass beads or plastic media can reduce harmful contaminant emissions while still achieving a smooth surface finish on metal parts.
Additionally, manufacturers in India may offer options specifically designed for heavy surface contaminants or to improve the quality of surface preparation needed for building materials, ensuring that every choice aligns with the desired surface finish and operational needs.
Guide to Shot Blasting Machines: Maintenance and Safety
Routine Maintenance Tasks
Operators of shot blasting machines should regularly check the dust collection system to ensure it is clean and functional, helping to remove contaminants and maintain air quality. They should inspect the blast wheel assembly and replace the abrasive materials, such as steel shot or aluminum oxide, when worn. It's important to examine the conveyor belt for wear and adjust it to prevent uneven blasting.
Maintenance tasks should typically be scheduled every few months, but operators must watch for signs of increased vibration levels, unusual noise, or changes in the desired surface finish. If a workpiece that was once smooth is now coming out with a rough surface profile, this may indicate the need for immediate attention. Regular checks on the storage hopper and blasting media are also necessary to ensure they are filled with the correct abrasive agent, whether it's glass beads or plastic media, for the blasting method used.
Performing these tasks not only prolongs the life of the machines but also helps keep operating costs in check for users, particularly for manufacturers in India working with large or delicate workpieces.
Safety Precautions During Operation
Operators of shot blasting machines should always wear personal protective equipment, including goggles, gloves, and ear protection, to ensure safety when using abrasive blasting methods. In case of an emergency or equipment malfunction, they must immediately stop the machine, alert supervisors, and follow the emergency procedures outlined in the safety manual. This includes safely shutting down the compressed air supply and checking the dust collection system for blockages.
To prevent unauthorized personnel from entering the shot blasting area, safety protocols must include clear signage, restricted access barriers, and training for all employees on the potential dangers. Operators should be particularly cautious when working with delicate workpieces and sensitive materials, as the high velocity of the abrasive materials like steel shot or aluminum oxide can cause serious harm.
For larger workpieces or heavy surface contaminants, using machines like wheel blasting machines or wet blasting machines with effective blast cabinet and storage hopper designs is important. Regular maintenance requirements should also be established to keep machines running safely and efficiently.
Future Trends in Shot Blasting Technology
Advancements in automation and robotics are set to improve shot blasting machines, enhancing their efficiency. Automated systems can operate conveyor belts, moving large workpieces through blast cabinets, while robotic arms manage delicate items to minimize damage. Manufacturers in India are likely to emphasize intelligent blasting methods, incorporating high-velocity centrifugal wheels and blast wheel assemblies for better results.
Environmental regulations drive the adoption of greener abrasive blasting practices. Innovations such as wet blasting machines and dust collection systems help reduce harmful emissions, while using recyclable materials like glass beads and plastic media lowers operational waste. Future shot blasting technology will also embrace smart technology and data analytics. This can optimize the selection of abrasive materials, analyzing grit size and shape to achieve the desired surface finish.
Sensors can monitor vibration levels and maintenance needs in real time, streamlining the tracking of equipment performance like steel grit or aluminum oxide handlers. The integration of dynamic separation systems ensures that different abrasive agents do not become contaminants, keeping processes clean and effective. These developments promise smoother surface finishes and more efficient blast cleaning of metal parts and building materials.
Final thoughts
Shot blasting machines are industrial tools designed for surface preparation and cleaning. They function by forcefully propelling abrasive materials at surfaces to eliminate contaminants, rust, and old paint, thereby improving surface finish and enhancing adhesion for coatings.
These machines are available in various forms, such as Wheel Blasting, Air Blasting, and Micro-Blasting systems. Wheel Blasting machines deploy a rotating wheel to launch abrasives, making them ideal for large-scale projects. Air Blasting machines use compressed air to project the media, offering versatility for smaller tasks. Micro-Blasting units feature a specialized nozzle for precision work, suitable for delicate surfaces.
The uses of shot blasting machines are broad. They are commonly employed in the automotive sector for cleaning and preparing parts, in construction for treating steel structures, and in aerospace for maintaining aircraft components. The marine industry also benefits from shot blasting in hull cleaning and surface treatment.
Grasping the principles, types, and applications of shot blasting machines is important for choosing the right system to address specific industrial requirements, ensuring effective outcomes in surface treatment processes.
FAQs
What are the basic principles of shot blasting machines?
Shot blasting machines operate on the principle of propelling abrasives at high speeds to clean, strengthen, or polish surfaces. Key principles include controlled blast patterns, optimal nozzle angles, and adjustable abrasive types. For example, use steel shots for heavy-duty cleaning and glass beads for delicate finishes.
What are the different types of shot blasting machines available?
Different types of shot blasting machines include tumble blasters for bulk parts, cabinet blasters for smaller items, and rotary barrel machines for complex shapes. Select based on your needs: for heavy-duty applications, choose a floor shot blaster; for precision work, opt for a cabinet system.
What are the common applications of shot blasting in various industries?
Common applications of shot blasting include cleaning metal parts in automotive manufacturing, preparing surfaces for coatings in aerospace, removing rust from construction materials, and enhancing the finish of castings in foundries.
How do I choose the right shot blasting machine for my needs?
Evaluate your project size, materials, and desired finish. For heavy-duty applications, consider a wheel blast machine; for delicate parts, choose a cabinet blaster. Assess production speed needs—automated systems increase efficiency. Research brands and read reviews to ensure reliability and support.
What maintenance practices are recommended for shot blasting machines?
Regularly inspect and clean the blast wheel, replace worn components, lubricate moving parts, check the air pressure, and ensure proper sealing of the machine. Schedule routine maintenance every 500 hours of operation and keep detailed logs of inspections and repairs for optimal performance.
Write a comment ...