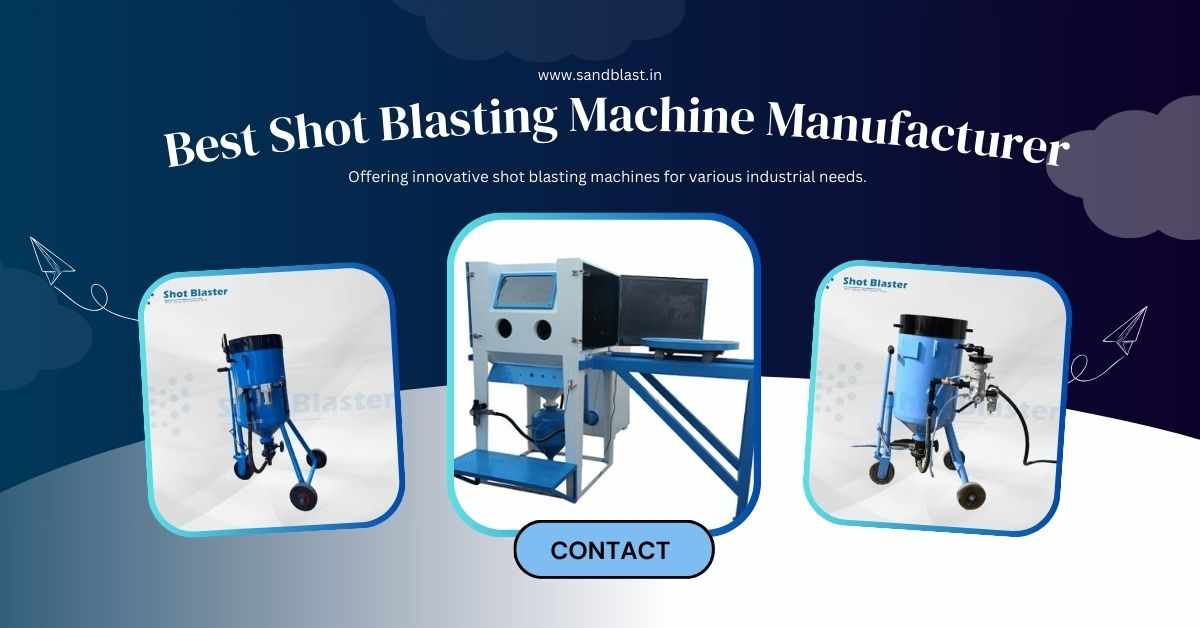
Shot blasting is an effective technique for cleaning and preparing surfaces made of metal, concrete, and more. This method employs steel shot propelled at high speeds to remove debris, rust, and imperfections. It enhances surface quality and prepares it for painting or coating. This article will discuss how shot blasting operates, its benefits, and its applications across various industries.
Gaining insight into this process can help you recognize its significance in manufacturing and construction.
Also Check – Shot Blasting Machine | Shot Blasting Machine Manufacturer | Buy Shot Blasting Machine
Overview of Shot Blasting Processes
Shot blasting processes rely on high-velocity abrasive materials propelled at the workpiece using a centrifugal wheel. This technique helps to remove imperfections like rust, mill scale, and debris on various materials, including metals and ceramics. The shape, size, and hardness of media types—such as steel shot or aluminum oxide—often determine how effectively the surface can be polished.
Different applications require specific methods; for example, grit blasting is used for more aggressive cleaning, while shot peening can relieve tensile stress in metals. Some environments may benefit from wet blasting, which reduces dust, while blast cabinets or blast rooms contain the process for safe operation. The choice of equipment, like shot blasters or blast pots, further influences efficiency, ensuring optimal performance during tasks like welding or deburring. Understanding these factors lays a foundation for a shot blasting guide to achieve the best results in surface preparation tasks.
Importance of Surface Preparation in Shot Blasting
Surface preparation is a necessary step in shot blasting processes that helps achieve the best results. When a workpiece is prepared properly, it allows the shot blaster to work effectively, removing imperfections like rust and mill scale. For instance, high velocity shot blasting with steel shot cleans metal surfaces efficiently compared to other methods like sandblasting and grit blasting.
If not prepared well, the surface could trap contaminants or have uneven textures, leading to poor adhesion of coatings and decreased performance over time. Specific methods, such as deburring and using the right media types, shape, size, hardness, and density, can enhance shot blasting efficiency.
Additionally, techniques like shot peening can improve tensile stress on metals while wet blasting reduces dust in sensitive areas. Employing blast cabinets or blast rooms allows for better control and safety.
Learn about - https://riyasingh258.stck.me/post/699684/The-Complete-Guide-to-Shot-Blasting-Machines-Principles-Types-and-Applications
Materials Commonly Used in Shot Blasting
Steel Shots
Steel shots are small, spherical particles that have unique characteristics making them effective for shot blasting applications. Their uniform size ensures even impact distribution, making them ideal for polishing and preparing metal surfaces. Compared to other abrasives like copper or aluminum oxide, steel shots are more aggressive and efficient, especially for tough tasks like removing mill scale and surface imperfections.
When selecting steel shots for a project, factors such as mesh size, hardness, and density should be considered. A finer mesh might be needed for smoothing surfaces, while larger sizes could be used for heavy-duty jobs.
Additionally, understanding the shape and velocity applied during the blast process helps achieve the desired results, whether in blast rooms or using portable blast pots. Steel shots are versatile and can accommodate various surface preparation methods, including deburring and shot peening, which enhances tensile stress on metals. The choice between steel shots and other media types depends on the specific application, making steel shots a popular option in both industrial and manufacturing settings.
Metallic Abrasives
Metallic abrasives, such as steel shot and aluminum oxide, are commonly used in shot blasting due to their distinct features and benefits. These abrasives are available in various sizes and shapes, facilitating effective surface preparation techniques like polishing and deburring, while efficiently removing defects such as rust and mill scale from workpieces. Their hardness and density influence how the media affects metal surfaces, allowing for high-speed operations in blast cabinets and pots.
In comparison to non-metallic abrasives used in sandblasting or wet blasting, metallic abrasives generally provide improved efficiency for demanding tasks like welding preparation and shot peening, which creates tensile stress on surfaces to improve strength. When choosing metallic abrasives, factors include the specific application, whether softer metals or ceramics are involved, along with the abrasive’s shape, size, and hardness, ensuring optimal outcomes without harming the workpiece.
This guide highlights the necessity of aligning the right abrasive with the task for effective surface cleaning and preparation.
Also Check – Shot Blasting Machine Price | Best Shot Blasting Machine
Non-metallic Abrasives
Non-metallic abrasives in shot blasting have numerous benefits compared to traditional metallic options.
For example, they are gentler on softer metals like copper, which helps avoid damage during surface preparation. With a variety of media types, such as ceramics and aluminum oxide, they enable precise polishing while reducing dust generation. The media's attributes, including size, shape, and hardness, significantly influence their performance; smaller mesh sizes excel in delicate tasks like deburring or cleaning ceramic surfaces, while larger sizes are suitable for more demanding needs like removing mill scale.
These abrasives particularly shine in industries such as automotive and aerospace, where they prepare metal surfaces for welding or coatings without leaving abrasive residues. They are also effective in wet blasting for limited dust and in blast cabinets and rooms for controlled use.
Get expert insights - https://riyasingh258.stck.me/post/699735/Choosing-the-Right-Shot-Blasting-Machine-for-Your-Industry
Types of Shot Blasting Processes
Airless Shot Blasting
Airless shot blasting offers numerous benefits compared to traditional sandblasting. By using a centrifugal wheel, it propels media, such as steel shot, at high speeds to clean parts more efficiently. This method is particularly advantageous in sectors like automotive and aerospace, where surface preparation is important for welding and achieving high-quality finishes.
Instead of grit blasting, which relies on angular shapes for aggressive cleaning, airless shot blasting uses spherical media types for optimal polishing and durability while preventing damage to soft metals like copper and aluminum. The principles of operation include adjusting the size, shape, and density of the abrasives to effectively target imperfections like mill scale on metal surfaces. Different setups, including blast rooms and blast pots, promote effective cleaning while minimizing the environmental footprint.
This approach also incorporates techniques like shot peening and can adapt to wet blasting, providing flexibility for tasks ranging from deburring to preparing ceramics for coatings. The option to recycle shot media boosts cost-effectiveness and reduces waste.
Suction Blasting
Suction blasting distinguishes itself from traditional shot blasting methods, such as sandblasting and wheel blasting, by using a vacuum to pull abrasive media toward the workpiece. This technique improves surface preparation by cleaning and polishing various materials, including metals, ceramics, and softer metals like copper. In industrial environments, suction blasting effectively removes flaws like rust and mill scale, while also prepping surfaces for welding or painting.
Notable benefits include lower dust production and improved control over abrasive application, leading to consistent outcomes. However, it may face challenges regarding the size of areas it can cover compared to blast rooms and cabinets designed for larger items. Suction blasting is often favored for precise tasks such as deburring or shot peening, making it important to select appropriate media types and consider factors such as shape, hardness, and density.
Employing materials like aluminum oxide or steel shot can amplify the impact on the treated surface, as emphasized in shot blasting resources.
Wet Shot Blasting
Wet shot blasting is a unique surface preparation technique that uses a centrifugal wheel and water to reduce dust during the cleaning of metal surfaces. This method effectively removes rust, mill scale, and surface imperfections from tough materials such as steel and aluminum. Automotive applications, including the preparation of car body panels, benefit significantly, as it ensures coatings adhere properly and protects softer metals like copper.
In construction, the process is useful for deburring and polishing, enhancing adhesion for paints and other coatings. The diverse sizes and shapes of abrasive media, such as steel shot and aluminum oxide, add to the flexibility of wet blasting, allowing operators to adjust density and mesh for specific requirements.
Additionally, it is beneficial in shot peening, which improves the durability of components by increasing tensile stress. Wet shot blasting provides an environmentally friendly option for achieving smooth surfaces while minimizing operational hazards.
Also Check – Shot Blasting Machine Manufacturers in India | Shot Blasting Machine for Sale
Applications of the Shot Blasting Process
Automotive Industry
Shot blasting is essential for preparing surfaces in automotive components by cleaning and smoothing the workpiece, which removes imperfections such as rust and mill scale. This process ensures a better bond for paints and coatings. Various media types, including steel shot and aluminum oxide, are propelled by a centrifugal wheel at high velocity.
Different media sizes and shapes cater to specific tasks, such as polishing surfaces and deburring, which enhance the overall quality and durability of vehicles. Advancements in shot blast technology and techniques, like wheel blasting and wet blasting, improve manufacturing by increasing efficiency and reducing production times. Challenges, like the risk of damaging soft metals such as copper and aluminum, are addressed through careful selection of shot hardness and density, as well as proper training in using blast cabinets and blast pots.
Moreover, modern shot blasting guides assist professionals in adapting the process to their needs, leading to improved outcomes in welding and shot peening applications.
Construction Industry
Shot blasting is a method commonly employed for surface preparation in the construction industry. It efficiently removes imperfections like rust and mill scale from metal surfaces. This is done using various types of media, including steel shot and aluminum oxide, propelled by a centrifugal wheel at high speeds. The process provides a clean and polished workpiece, enhancing the stickiness of paints and coatings.
In welding, shot blasting readies surfaces by removing debris, thus elevating the quality of the weld.
Additionally, shot peening helps in strengthening metals by creating tensile stress, which increases their durability. Different shapes and sizes of abrasive media can be selected based on project requirements, while methods such as wheel blasting or wet blasting address specific needs. Environmentally-friendly practices are also significant, as dust and waste generated during shooting can impact air quality. Employing blast cabinets or pots can help contain debris, ensuring safer operations and lessening environmental impacts.
Also Check – https://rb.gy/ii4tpg | https://rebrand.ly/SB5asln | https://rebrand.ly/SB49Ind | https://cutt.ly/Ge9OZ25U
Benefits of Shot Blasting
Shot blasting offers notable advantages in preparing surfaces and enhancing material durability, making it an effective choice for various industrial applications. It employs a centrifugal wheel to propel different types of abrasive media, such as steel shot and aluminum oxide, at high speeds onto a workpiece. This process cleans surfaces, removes imperfections such as rust and mill scale, and increases durability.
Shot blasting is frequently favored over sandblasting due to its aggressive nature, which treats tougher materials and improves tensile strength through shot peening.
Environmental Considerations in Shot Blasting
Shot blasting processes can have environmental impacts depending on the types of abrasive media used.
For example, steel shot or ceramics generate less dust compared to grit blasting with harsher abrasives. High velocity from a centrifugal wheel can disperse particles into the air, potentially causing pollution. Wet blasting methods help address this issue by using water to trap dust and reduce airborne particles, making it preferable in settings where air quality is important.
Compliance with environmental regulations can be achieved by implementing proper dust collection systems in blast rooms and blast cabinets, which capture hazardous waste materials.
Additionally, choosing media with lower hardness and density helps minimize damage to the workpiece while maintaining effectiveness. Regular monitoring of operations with shot blasters and blast pots can assist in managing media types and sizes, ensuring they are suitable for the job without harming the environment.
Safer operations such as shot peening can also be considered, as they reduce material waste and promote longer product lifespan, benefiting both environmental considerations and project efficiency.
Common Challenges in Shot Blasting Processes
Operators often encounter challenges such as dust generation, equipment wear, and improper settings during shot blasting processes. These obstacles can significantly reduce overall efficiency and impact the quality of the workpiece. Variations in abrasive materials, like steel shot or aluminum oxide, can affect results; the size, shape, and hardness of these media types determine how effectively surface preparation removes imperfections.
For instance, larger mesh sizes provide aggressive cleaning, while finer materials are more suitable for polishing. Environmental factors, including humidity and temperature, may also complicate shot blasting by affecting dust collection systems in blast rooms and the operation of blast pots.
To address these challenges, setting up appropriate dust collectors and selecting the right shot blaster settings are important. Techniques like wet blasting can help reduce dust issues, while ensuring proper abrasive selection enhances performance.
Furthermore, maintaining equipment lowers the risk of contamination that could cause surface defects, particularly when working with delicate materials like ceramics or soft metals such as copper.
Future Trends in Shot Blasting Technologies
Future trends in shot blasting technologies include advancements in automation and robotics. As shot blasters become more computerized, they improve surface preparation methods, allowing for consistent and efficient polishing of workpieces with minimal imperfections. New materials and eco-friendly abrasives, such as aluminum oxide and various organic substances, will enhance the sustainability of processes like grit blasting and wet blasting while ensuring high velocity and surface quality.
Innovations in shot peening will focus on reducing tensile stress on metals and ceramics without causing environmental harm.
Additionally, integrating technologies like IoT will enable users to monitor blast cabinets and blast pots in real time, allowing for optimal adjustments in abrasive size, hardness, and density while enhancing control over the shape of individual particles. These advancements are likely to improve efficiency in addressing challenges like mill scale removal and deburring in industries such as welding, while ensuring that soft metals like copper can be processed safely.
Write a comment ...